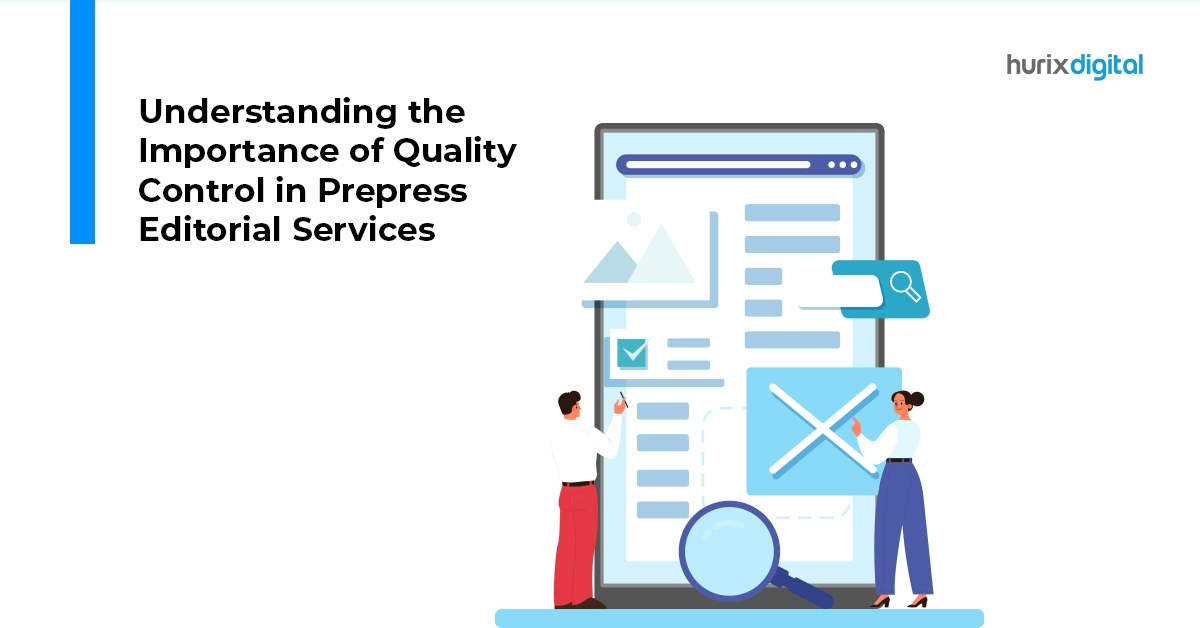
Understanding the Importance of Quality Control in Prepress Editorial Services
Prepress is a crucial stage in the publishing and printing industry where editorial content is scheduled for final production. To guarantee that the content is precise, visually aesthetic, and ready for publication, this step entails several procedures, such as typesetting, proofreading, formatting, and image adjustments.
Prepress editorial services must include quality control because it guarantees that the final output will be accurate and of the highest caliber.
This blog examines the benefits, procedures, and best practices related to quality control in prepress services. Read on to explore more!
Table of Contents:
- What are Prepress Services?
- Role of Quality Control in Prepress Services
- 7 Key Procedures Associated with Quality Control
- Best Practices for Implementing Quality Control in Prepress Services
- Takeaway
What are Prepress Services?
The methods and procedures that take place between the development of a print layout and the final printing are referred to as prepress in the print and publishing sectors.
Illustration curation for press, choice of media, editing, quality control inspections, and, if necessary, printing plate creation are all included in the prepress process.
Also Read: The Latest Trends in Prepress Services: What You Need to Know
Role of Quality Control in Prepress Services
Making sure the content is flawless, consistent, and of the highest caliber before it is printed is the main goal of quality control in prepress editorial services.
This includes proofreading for spelling and grammar mistakes, making sure the formatting is correct, examining the quality of the images, and making sure the content is accurate and in line with the intended layout.
Prepress editors can identify possible problems early in the process and address them before the final product is produced by putting strong quality control procedures in place.
7 Key Procedures Associated with Quality Control
Prepress editorial services use quality control to make sure the content satisfies predetermined editorial standards through some procedures and inspections. These procedures could consist of:
1. Proofreading
An essential part of quality control is proofreading, in which editors carefully go through the text to fix any typos in grammar, punctuation, or spelling. Even following the initial proofreading, there is typically some likelihood of errors occurring, which can become evident during the typesetting and design stages of the project.
Proofreading processes guarantee that the text is lucid, cohesive, and error-free, all of which could affect the final product’s readability and reliability.
2. Verification of Images
Images are essential for improving printed materials’ visual appeal. Editors are responsible for ensuring that all images are high-resolution, correctly aligned, and in the appropriate size and format during quality control.
Choosing the incorrect resolution for an image is a frequent mistake in prepress printing. Selecting an image resolution of between 250 and 300 dpi (dots per inch) is the best option.
In addition to resolution, it is important to ensure that the selected images are not resized (either maximized or decreased) by over 20% of their original size, as this can have an impact on resolution. Erroneous resizing of the images may also result in different preparation problems before the copy is sent for final printing.
3. Formatting Check
To keep the content’s overall look and feel consistent, prepress editorial services must use consistent formatting.
Editors must make sure that all formatting elements, including headings and subheadings, are consistent and adhere to the established style guidelines. To keep the formatting consistent, any variations from the rules must be fixed.
4. Color Management
Color management is the method of regulating and preserving color accuracy from layout to the finished printed product at every step of print production. Ensuring that the colors displayed on the computer screen properly correspond to the colors printed on the finished product is the goal of color management.
The three primary steps in the color management process are conversion, calibration, and profiling. Using color management tools in the prepress workflow is crucial to ensuring that color management is applied correctly in the field.
5. Accuracy of Content
In prepress editorial services, content accuracy is of utmost importance.
Editors must ensure that all facts, figures, and information included in the content are accurate and latest. It is imperative to rectify any errors or discrepancies to avoid the spread of disinformation and preserve the credibility of the finished output.
6. Optimize Font Spacing
For print publishing to be as successful as possible, text spacing must be optimized. The best approach in this case is to adhere to traditional typographic practices, like modifying your text to produce a distinctive appearance that sets your design apart from competitors.
Making your writing look attractive and cohesive while taking into account different elements like letters, punctuation, paragraphs, and negative space is the goal here.
7. Select the Appropriate Paper
Successful print publishing greatly depends on the choice of paper. Once you have all the design aspects put together and are just one step away from submitting your final layout to print, this is an essential component that you should take care of.
To help with the selection process, keep in mind that different kinds of print paper have distinct feels and looks, so it’s crucial to choose one that suits your work, genre, and budget.
Best Practices for Implementing Quality Control in Prepress Services
Following are some of the best practices crucial for implementing quality control in prepress editorial services:
1. Creating Standard Operating Procedures (SOPs)
Developing standardized quality control processes and workflows can help guarantee effectiveness and uniformity in the prepress editorial process. SOPs should specify the procedures for quality control, the duties and responsibilities of team members, and the standards by which the content will be judged.
2. Performing Numerous Review Rounds
Multiple rounds of review should be part of prepress services to efficiently identify errors and inconsistencies.
Various team members can evaluate the material at different phases to offer new insights and spot any problems that may have gone unnoticed. The general quality of the content can be raised with the aid of collaborative review procedures.
3. Using Software and Automated Tools
Software and automation tools can help prepress editorial services’ quality control procedures to run more smoothly. Grammar checkers, spell checkers, and formatting software can help find mistakes more swiftly, freeing up editors to work on more complex quality control tasks.
4. Having Effective Client Communications
Prepress services must have open lines of communication with clients to comprehend their needs, wants, and expectations. Ensuring that the final product is in line with the client’s vision and goals can be achieved through periodic notifications, meetings for feedback, and progress updates.
Check out EXCLUSIVE: Hurix Mini-Book: PrePress Tips You Won’t Find Anywhere Else
Takeaway
Prepress workflow can be ensured, and quality control can be streamlined by using automation tools, following best practices, creating standardized procedures, and performing several review rounds.
Hence, producing aesthetically pleasing and error-free printed materials that appeal to clients and readers requires an in-depth understanding of quality control in prepress services.
If you are looking for immaculate and efficient prepress services, get in touch with Hurix Digital. We guarantee that you receive the finest solutions as we have extensive experience offering prepress services to our international clientele. Our products are based on four solid pillars: affordability, subject matter expertise, creativity, and accuracy.
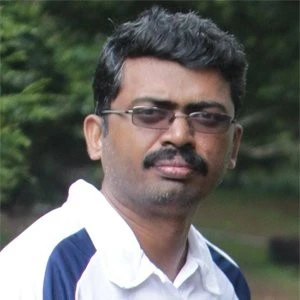
Vice President – Digital Content Transformation. He is PMP, CSM, and CPACC certified and has 20+ years of experience in Project Management, Delivery Management, and managing the Offshore Development Centre (ODC).